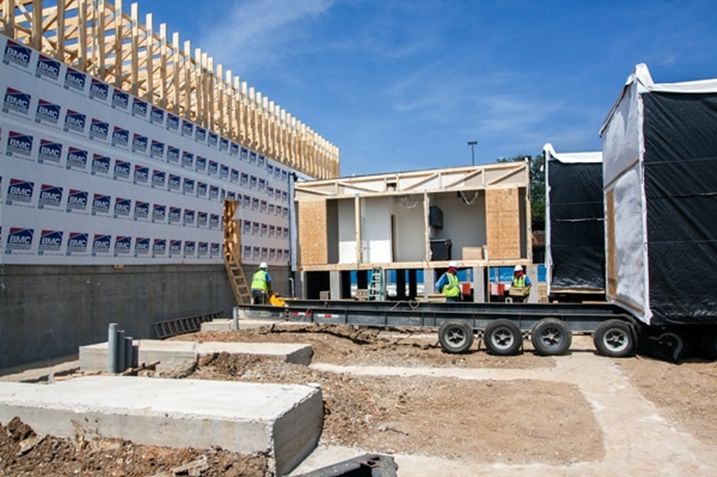
Workers with Ramtech assembling a commercial building through modular construction.
For years, Place Properties developed its apartments the traditional way: find a site, bring in the materials and use crews to build it from the ground up. But Place CEO Cecil Phillips is now all-in on a new way of developing apartments: assembling them in a factory hundreds of miles away, then putting the pieces together like a puzzle on the site.
The method is called modular construction. Phillips calls it the future of the housing industry, and he’s placing a more-than-$30M bet that he’s right.
“America, like in a lot of other places, we want what we want, we want it right away,” Phillips said at a Bisnow event in Atlanta last week. “Modular construction does more to scratch that itch, if you will, than traditional construction ever will.”
Place Properties owns and operates 3,200 apartment units in Georgia, Texas, Oklahoma, North Carolina and Virginia and has developed or owned 50,000 student housing and military housing units since 1995. It is putting the finishing touches on its first modular housing project in Atlanta and has plans to break ground on its first modular townhome project this spring.
The firm is also in talks to acquire a site in Metro Atlanta where it plans to build a 125K SF modular housing manufacturing facility, Phillips said. He declined to disclose the specific location until the deal is finalized. He said he’s formed partnerships to help fund the development, which he expects to cost $32M, factoring in the factory’s equipment.
Phillips expects to spend $3.3M a year to operate the plant, including training workers prior to opening. At full operation, Phillips expects the factory to employ upward of 200 people and will be able to produce a single-family dwelling every three to four days and eight apartment units a day.
The plant would not only be used for Place projects, but also be open to third-party developers and owners of housing and apartments. The plant will have a trade area of up to 850 miles, meaning it could service as far north as New York City and as far west as Austin, Texas.
The plant is just the start: Place plans to roll out a series of similar plants across the country.
“If we can prove the concept in Atlanta, we will be able to take this in short order to Philadelphia and Texas and Charlotte,” Phillips said.
The plans are ambitious, but Place Properties isn’t the only one preparing for a future where a greater share of U.S. apartments are built in factories.
Modular On The Rise
While modular construction only accounts for nearly 5% of all commercial construction, multifamily is the fastest-growing segment within the modular construction industry, according to the Modular Building Institute, an industry trade association. In 2017, manufacturers built a little more than 1,100 modular apartment units in the U.S. In 2018, that number more than doubled to 2,300 units, MBI Executive Director Tom Hardiman said. While data for 2019 is not yet available, he expects that number to grow even more.
“Really, the big difference is the blurring of the lines between a modular-built project and a site-built project,” Hardiman said. “Once you’re inside an apartment or hotel room, they’re all pretty identical. So why not make them in a factory?
With demand rising for modular construction, especially for pre-built apartments and hotels, some big general contractors are launching their own modular divisions, including PCL Construction in Canada, Chicago-based Skender and EllisDon, which is building Canada’s largest modular manufacturing facility in Ontario.
“That’s where we’re seeing the big opportunities,” Hardiman said. “So much so where some of the big GCs are starting to say, ‘We’re going to open our own modular factory.’”
For developers, modular’s premise sounds like a siren call: delivering a project for fewer dollars and in less time than via traditional construction. Phillips said once operational, Place Properties’ plant can develop a 12-story conventional apartment project for $140 per SF in six months. A traditional project would take upward of 24 months at a cost of $220 per SF, he said.
“A permanent competitive advantage for modular is the schedule,” Phillips said. “You can have your project done in six months [rather] than 24 months … and start generating income sooner. You don’t have to be a rocket scientist or even a developer to know what choice you’re going to take.”
Place wouldn’t be the first developer to use its own modular construction factory. Forest City (which sold to Brookfield Asset Management in 2018) built a modular factory in 2012 in the Brooklyn Navy Yard, in a partnership with Skanska USA, with plans to build more than a dozen apartment towers in the 100K SF facility.
Forest City executives claimed they had “cracked the code” on modular construction. The first out of the gate was 461 Dean St., a 32-story apartment tower that is among the tallest modular projects in the world. But a bitter dispute with Skanska over the plant and construction design caused the project to take four years, far longer than it would have with traditional methods. As construction on the building was wrapping, Forest City bought out Skanska and put the plant on the market, declaring it was out of the modular construction business. It ultimately sold it to the executive who led its modular division, Roger Krulak, for an undisclosed price. His spinoff company, FullStack Modular, is now making affordable housing units at the Navy Yard plant for developers working with the city’s Department of Housing Preservation and Development.
The Looming Labor Cliff
For years, labor costs have been increasing. But instead of it being a symptom of such factors as commodity price inflation or workers just too busy with other jobs, the issue is more systemic: Skilled construction laborers are aging and fewer are entering the industry to replace them. That makes the rapid inflation of construction costs more of a paradigm shift than a temporary blip, experts say.
Construction costs have been steadily rising each year since the Great Recession, exceeding 5% per year since 2017, according to data compiled by Turner Construction Co. Just this week, the Arthur M. Blank Family Foundation vowed to donate $5.7M to a Georgia organization aimed at creating a pool of skilled labor, citing the sizable need for more specialized workers. The Georgia Department of Labor estimates 271,529 skilled jobs will be needed by 2022, according to The Atlanta Journal-Constitution.
While labor shortages drive up the cost of construction, many municipalities are clamoring for more affordable housing. But developers say they can’t build it and turn a profit without heavy subsidies.
“I think a lot of folks are going to modular because it’s difficult to navigate the marketplace for laborers,” said Roland Brown, a vice president at modular construction firm Ramtech Building Systems. Issues of labor are lessened on a factory floor, Brown said. Even skilled workers have more longevity in a job with benefits and more assured employment than at a subcontractor. Brown said over half of Ramtech’s 60 factory workers have been with the company 15 years or more. Plus, the skill requirements are lessened in modular construction, he said.
“You don’t need an auto mechanic to build a car. You don’t need a computer scientist to build a computer,” Brown said. “Not everyone needs to be a master carpenter to do a wall assembly in a factory.”
No comments:
Post a Comment